
The discharge of dirty water from wet screens, sand screws or classifiers has always presented numerous challenges to sand washing operations. While the use of settling ponds is typical, the method unleashes a host of disadvantages. Pond maintenance is costly, time consuming, and hazardous to equipment and personnel. Water resources are not adequately recycled and production is potentially stalled if dirty water gets back to the plant – pushing sustainability further from reach.
Importantly, amidst today’s restrictive permitting environment, wash plants are commonly locked into limited footprints that simply cannot accommodate a series of ponds. Additionally, water may be scarce for some operations; while others may not have a significant budget for high-dollar dewatering devices such as hydrocyclones, belt presses, and plate and frame presses.
Consequently, companies must innovate to create sustainable, affordable, and efficient wash water management solutions. The latter is illustrated by a recent collaboration between Wendling Quarries, Inc. and Clearwater Industries, two companies who employed “a teamwork approach” to engineer a clarifying and sludge thickening system that delivers highly cost-effective wash water clarification.
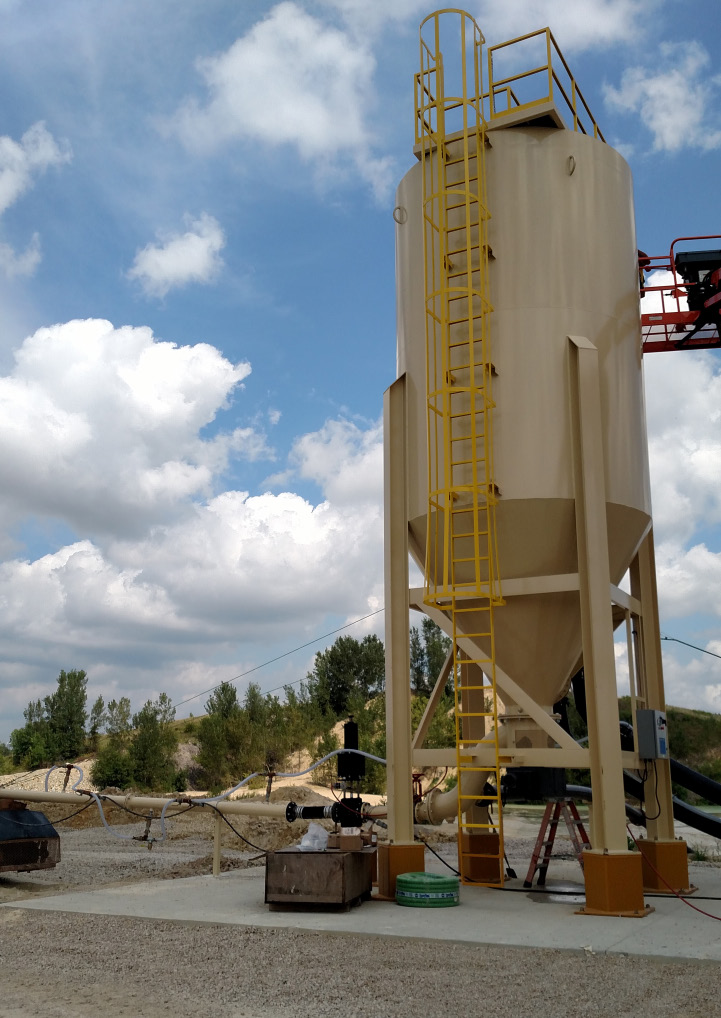
Wendling Quarries operates nearly 100 quarries in its 14-county region throughout Eastern Iowa and Western Illinois. “Our Cedar Rapids South Quarry faces a footprint constraint that requires proper clarification to pump out clear water on one end, and a high percentage of solids on the other,” says Wendling General Superintendent Steve Yerington. He explains that the plant was operating an older, existing clarifier and even after some experimentation with flocculants, results remained inconsistent. “We could not get a consistent mud discharge from the old clarifier; and we were seeing a low percentage of solids. The system was not operator-friendly. It needed to be monitored constantly as it would either flow too rapidly, or would solidify and plug up,” he says, stressing that the situation would take his operator away from the wash plant for far too much time.
Yerington contacted Clearwater Industries to investigate a potential solution. Clearwater was founded in 1996 by Bob Gralton of Mequon, Wisconsin. The company specializes in the design of polymer preparation systems, water clarifiers, and fines recovery systems.
Strategic & Tactical Solutions
“Our strategy involves analyzing the application, evaluating the existing system and methods, and recommending the tactics and technologies that will deliver the desired results,” says Joe Lamb, application engineer for Clearwater Industries. He adds that it’s been a joint effort with Wendling Quarries, working closely together on analysis, experimentation, lab testing, field testing and ongoing design improvements.
For the Wendling site, the new custom-engineered sludge thickening clarification system has dramatically increased the percentage of solids in the discharge. With their prior setup, the percentage of solids averaged in the lower 20s. The new system ensures a consistent average of 64 to 68 percent solids, with solids as high as 77-percent depending upon the material feed.
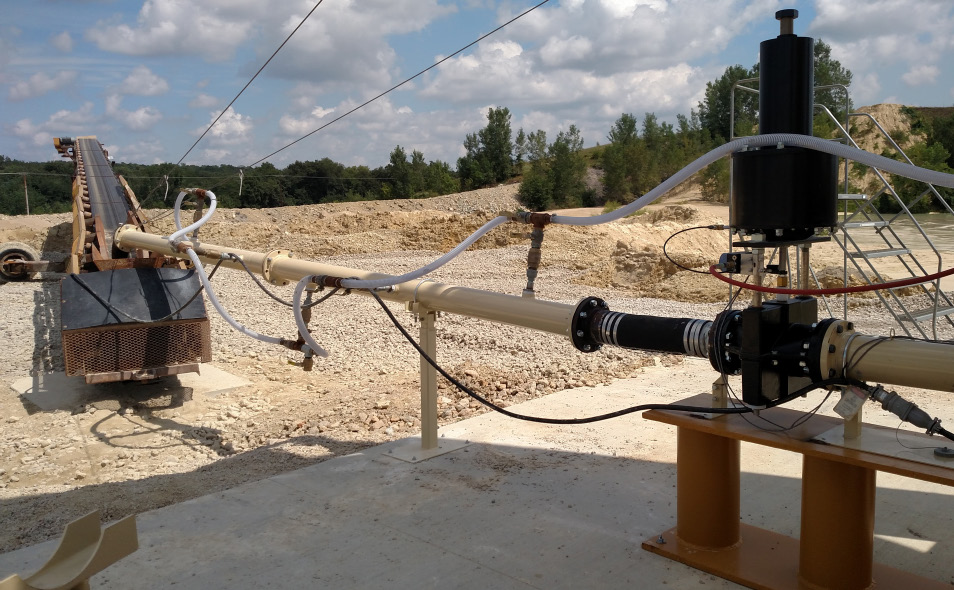
To keep the system simple and user-friendly, Yerington wanted to stick with a single 13,000-gallon clarification tank. The dirty process water is pumped into the clarifier as flocculant is added via an automated system. Very clean water overflows the top of the clarifier and can go right back to the plant for reuse. The underflow, or thickened mud is discharged and is ultimately transferred to a final resting place. “Now we can convey the discharge material 100-feet to an initial containment area where it dries in less than a week. Eventually we will pump the material rather than using a conveyor,” says Yerington.
Clearwater’s automated flocculant system, says Lamb, is dosing the polymer automatically based upon the varying solids level. “That is such a critical issue as the right chemistry must exist to allow the clarification process to work,” he says. Also, he stresses that the operation had been using a two-part-chemistry treatment that included a very expensive cationic component. “After our lab tests, we could provide a single-source flocculant that is far more cost-effective in treating at the top of the tank for clear water overflow, while also treating at the bottom to allow the sludge to dewater more quickly,” says Lamb.
Key Feature
One of the key features of the new system, says Yerington, is the tri-arm variable-speed rake that aids in thickening and maintains the consistency of the mud. A pressure-sensitive gauge on the rake monitors the mud level.
As that mud level reaches a designated point, a pinch valve is activated to discharge the material. Yerington goes on to explain that a meter on the pinch valve reads the width of the valve opening, allowing the automated flocculant system to properly dose the solids again as the material enters the discharge pipe.
“Maintaining the proper mud level is so important,” he says. “The compaction of the mud squeezes out the water but if the mud level is too high, the solids will not settle out and the clean water does not go over the weirs.”
The operation is washing four different benches in the quarry. “Each bench offers a differing recipe – so we refine the flocculants that go in and we refine the speed of the rake. We might also have to adjust the mud level to get our desired results. Now that we get consistent results, the fine tuning really makes a difference,” says Yerington. He has created a spreadsheet that notes the material feed per bench, thus dictating the required operational settings of the clarification system per bench. “This allows me to properly monitor the results, making needed adjustments as we go along. We want to pinpoint the consistency even more closely,” he says.
Lamb says that Clearwater is more than an equipment and polymer supplier. “We are a business resource with the ability to analyze dirty wash water. We do a particle size distribution test and a percent of solids test to determine the most cost-effective solution for the plant. These tests will tell producers how many tons of fine sand can be recovered as a dry stackable material, and how many tons of fine silt and clay will be treated with flocculant,” he says.
It’s said that “strategic thinking is the what and why, while tactical thinking is the how.” In creating this custom-engineered system, Wendling Quarries and Clearwater Industries clearly identified the what, why and how of cost-effective wash water clarification.
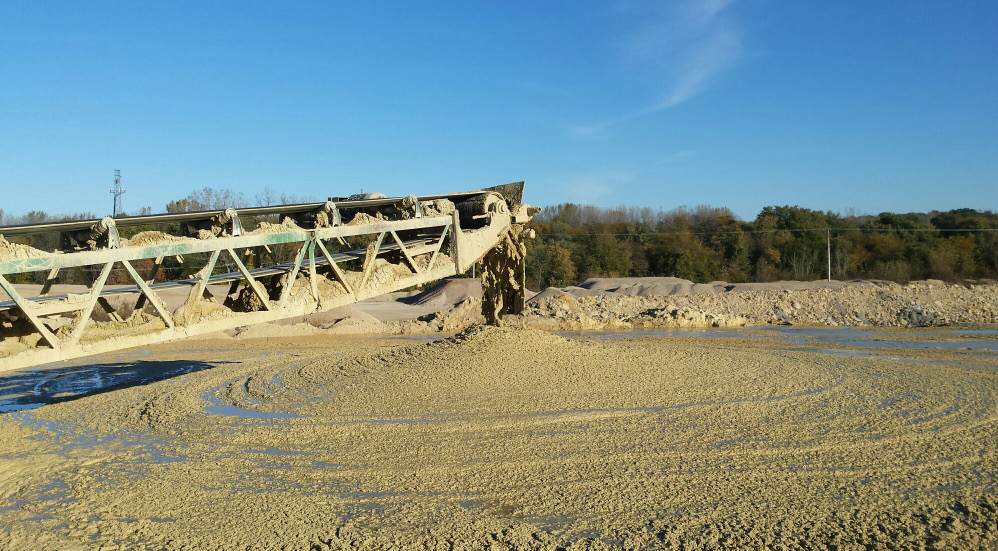
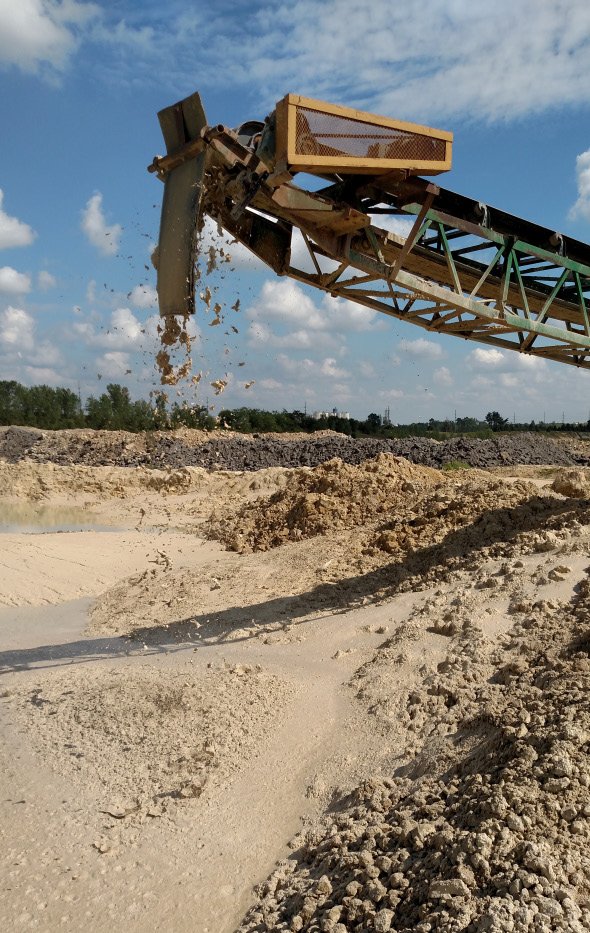