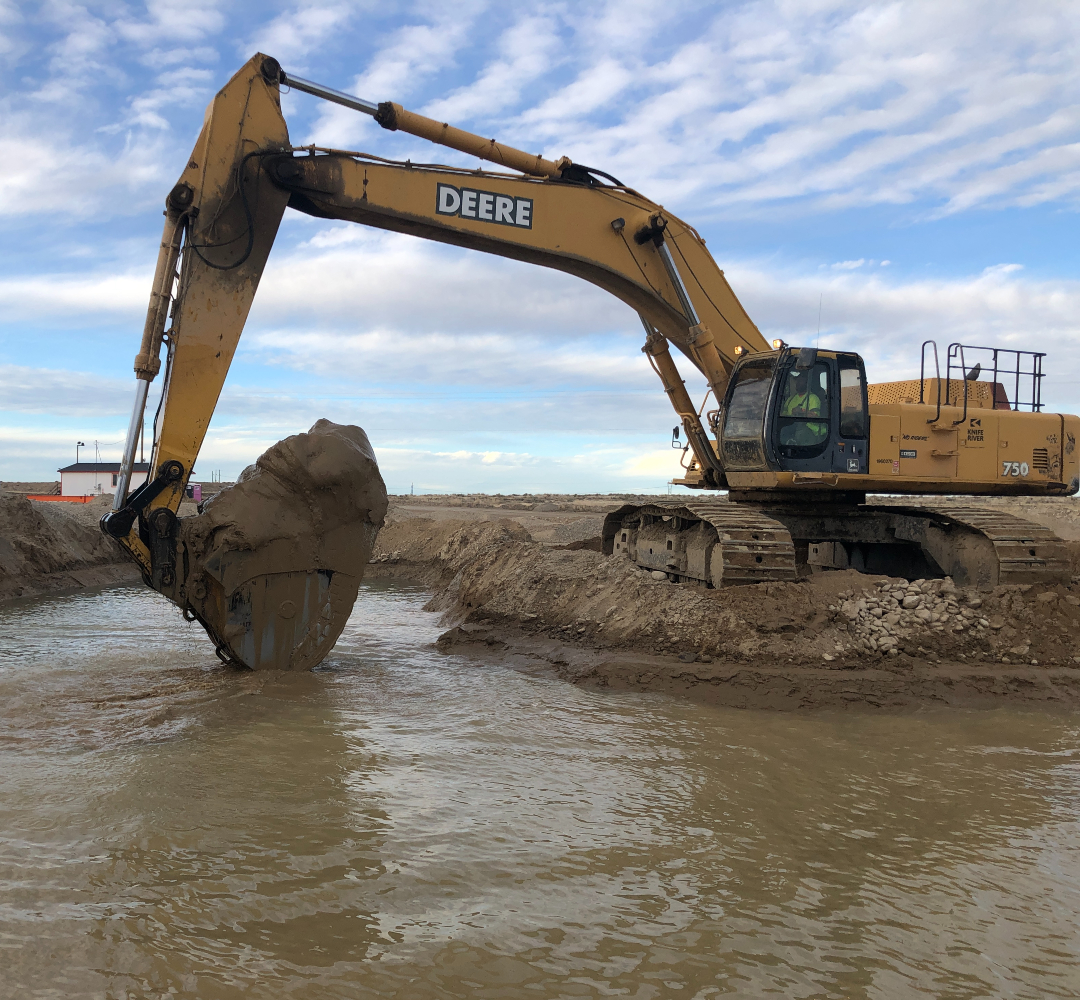
Company: Knife River
Location: Boise, Idaho
Challenge: Remove solids and unwanted fines from process water for reuse. Reduce settling pond footprint. Decrease pond cleaning time.
Treatment: Coagulation and flocculation in settling pond.
Capacity: 1,600 GPM
Unit Type: LQ50 Liquid Coagulant Dosing System, M500SS Dry Polymer Make-Down System
Results: Reduced turbidity by 87%. Settling velocity = 40 in/min
Benefits: 1,600 GPM of reused process water for the wash plant. Reduced settling ponds from 5 to 1. Decreased pond clean–out times significantly.
Knife River is a large construction material and contracting business with locations in 14 states throughout the western, central, and southern United States. They build critical infrastructure, including roads and bridges, and produce the aggregates, asphalt, and concrete needed for their jobs.
The Boise, ID, location produces washed aggregates for concrete production and other uses. The site runs about 22,000 tons per month of crushed product through its aggregate wash plant using 1,600 GPM of wash water.
Challenge
The site contains decomposed granite, causing high levels of TSS and colloids in their wash water. Despite flowing the slurry through a series of five settling ponds, the process water still contained solids and fines when it entered the clean water pond, which caused Knife River’s product to be out of spec.
Further, they had to clean out their ponds daily with an excavator, which took up valuable time due to soupy buckets. The material required further dewatering before being hauled off, and sometimes the material would have to be handled several times before going into a hauler truck. This process wastes valuable water, time, and operating costs.
Solution
In 2019, the Knife River Boise, ID, location contacted Clearwater Industries to explain their problems with their process water. Clearwater collected samples of their slurry and quickly determined the top-performing chemistry for their site.
With the proper use of coagulants and flocculants, Clearwater removed the solids and reduced turbidity from 610 NTU to 80 NTU (87%). Further, we achieved a settling velocity of 40 in/min, allowing the solids to quickly drop out of liquid suspension.
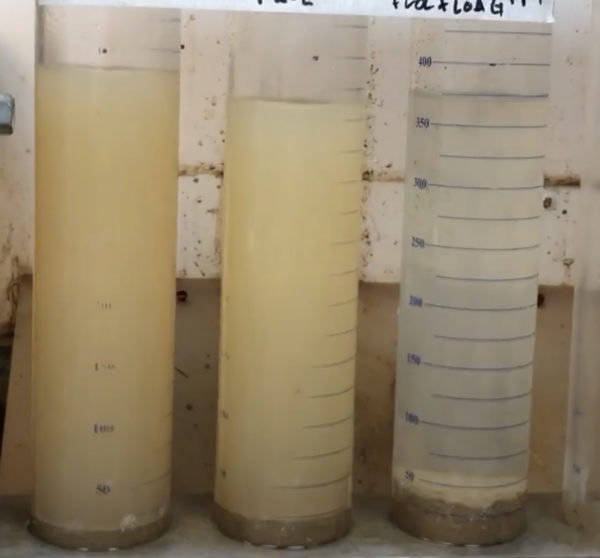
Image: Left to right; control, polymer flocculant only, coagulant and polymer.
To achieve these results on-site and at scale, Clearwater installed an LQ50 Liquid Coagulant Make-Down System and an M500SS Dry Polymer Make-Down System.
The LQ50 Liquid Coagulant Make-Down System continually prepares and doses the coagulant at a consistent strength and rate. The system runs continuously, and VFD controls allow the operator to adjust the dosing rate. A neat coagulant pump, dilution water pump, and in-line static mixer automatically dilute the raw coagulant to the desired solution strength.
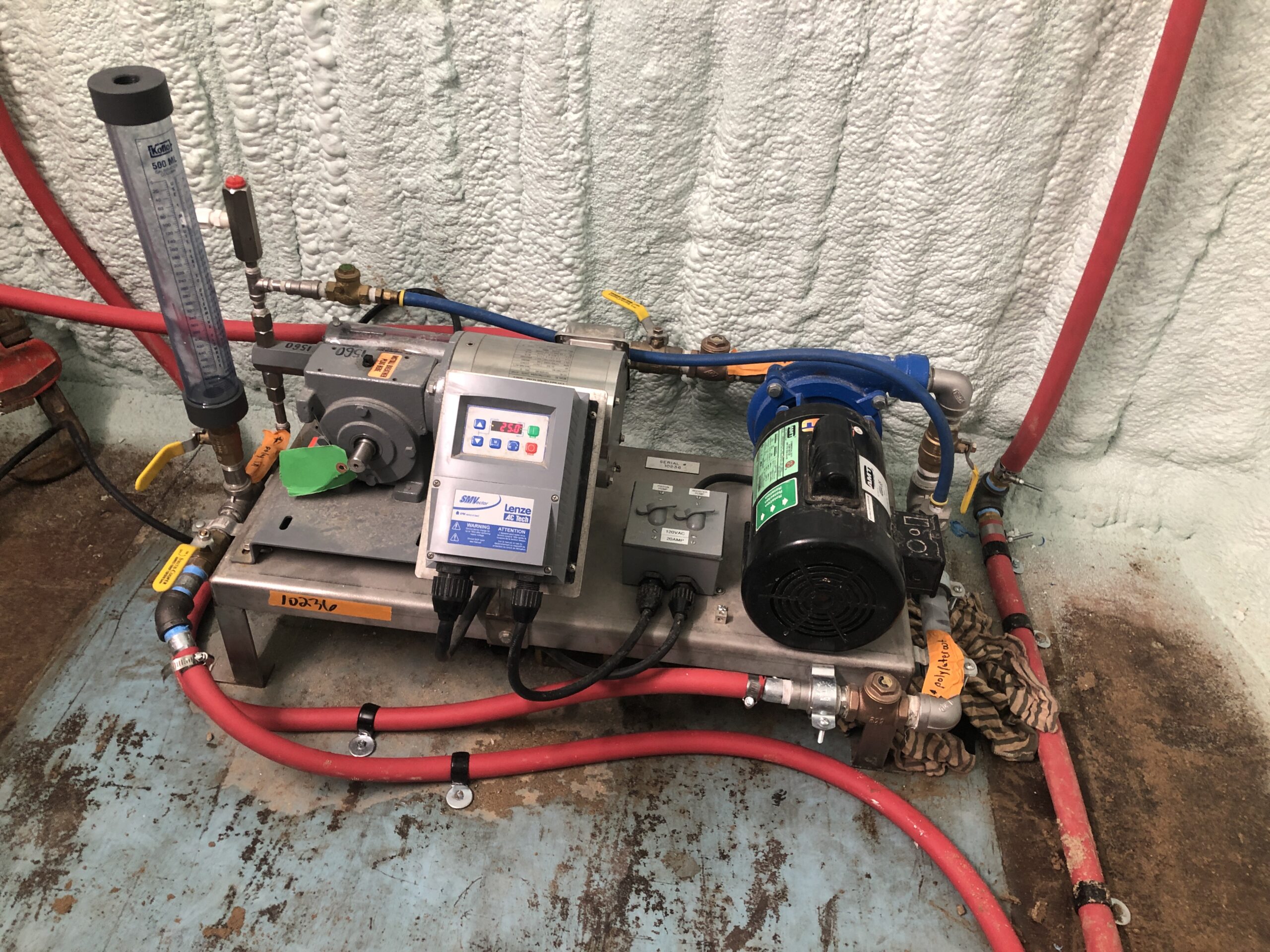
LQ50 Liquid Polymer Dosing System
The M500SS Dry Polymer Make-Down System automatically prepares and doses the polymer flocculant at a consistent strength and rate. The Hand/Off/Auto switch control panel allows the operator to set the system in auto or manual control. An ultrasonic-level sensor, VFD-controlled screw feeder, dilution water solenoid valve, and dilution water flowmeter automate the batching process providing a consistent solution strength with minimal operator attention required. The operator only needs to ensure dry polymer is in the hopper.

M500SS Dry Polymer Make-Down System
Clearwater worked with the site crew during commissioning to determine the optimal dosing locations. Dosing the coagulant in the sand screw overflow provides the necessary mixing energy for effective coagulation. In contrast, the polymer is dosed at the end of the slurry discharge pipe for optimal flocculation without the risk of over-shearing the flocculated solids.
Results
Upon installing the system, Knife River observed immediate results. First, the solids dropped out of liquid suspension quickly, sending clean water to their wash plant for reuse. This allowed them to maintain production time and pull less water from the ground.
Next, they increased their production space by reducing their settling ponds from five to one. Because the solids dropped out of liquid suspension within a few feet of the slurry discharge pipe, Knife River no longer needed as much retention time from their ponds.
Lastly, they significantly reduced the time it takes to clean their settling pond. The agglomeration of solids increases compaction at the bottom of the pond, which helps dewater the material. The compacted mud allowed operators to increase the volume of material per excavator bucket load, which decreased the time required to clean the pond. The material requires less handling and can be loaded directly into a hauler truck.
As of 2022, Knife Rivers chemical dosing systems continue to operate effectively. The plant reclaimed land previously used for settling ponds and put it to better use. They’ve also saved significant amounts of labor, diesel, and time by having more easily handled solids.
Call us today at 414-365-1200 to learn more about how we can improve your tailings management process.