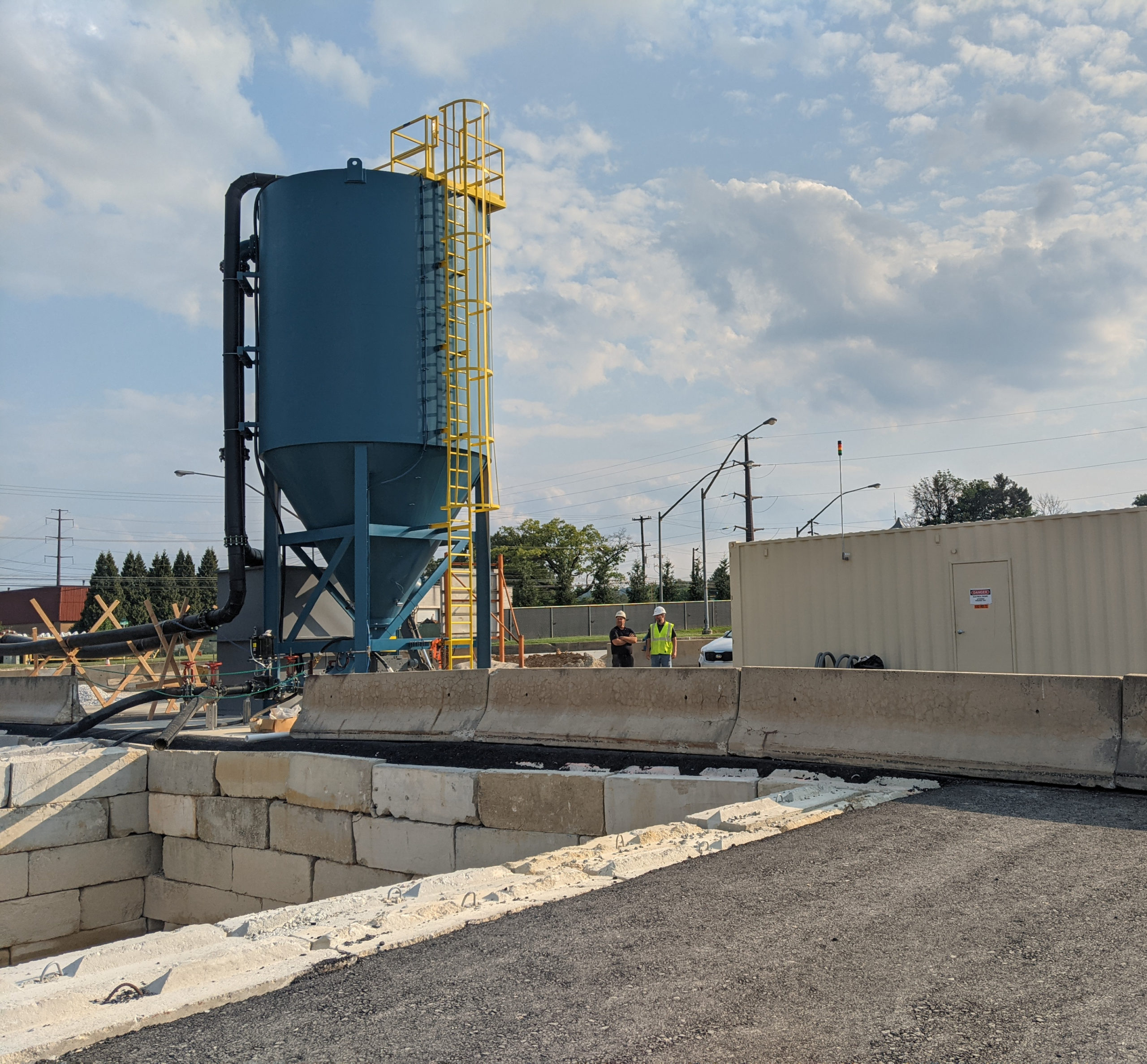
Company: Glasgow, Inc.
Location: King of Prussia, Pennsylvania, USA
Challenge: Eliminate settling pond to access material. Return clarified process water for reuse.
Treatment: Flocculation & High Compaction Clarifying Thickener
Capacity: 1,800 GPM
Unit Type: Sump & Slurry Pumps, LQ50, M800SS, Dilution Water Filter System, AutoFloc Dosing System, CW1400HC, Decant Water Sump
Results: 55%+ w/w mud, 90%+ clean water for reuse
Benefits: 4-5 million tons of material accessed for sale. Time and money saved from mucking settling pond.
Glasgow, Inc is a heavy industry and highway construction company servicing Pennsylvania, New Jersey, and Delaware. They serve the private and public sectors with projects that include airports, parking lots, highways, utilities, dams, nuclear power plants, and more. To meet the demand for their services, the company operates several asphalt plants and quarries, including the McCoy Quarry.
Challenge:
Glasgow’s McCoy Quarry is a limestone quarry that processes 300 tph of crushed limestone through its aggregate wash plant. The quarry is located in an urban area within the town of King of Prussia just outside of Philadelphia. Due to its metropolitan location, Glasgow couldn’t expand the quarry’s footprint and could only access the material within the current site, which was becoming a challenge.
Most of the quarry’s remaining material lay beneath the historic settling pond and production staging area. Much of the quarry reached the water table, and Glasgow couldn’t move their settling pond to another location on the site. It was clear that they had to remove their settling pond to access material and extend the life of their quarry.
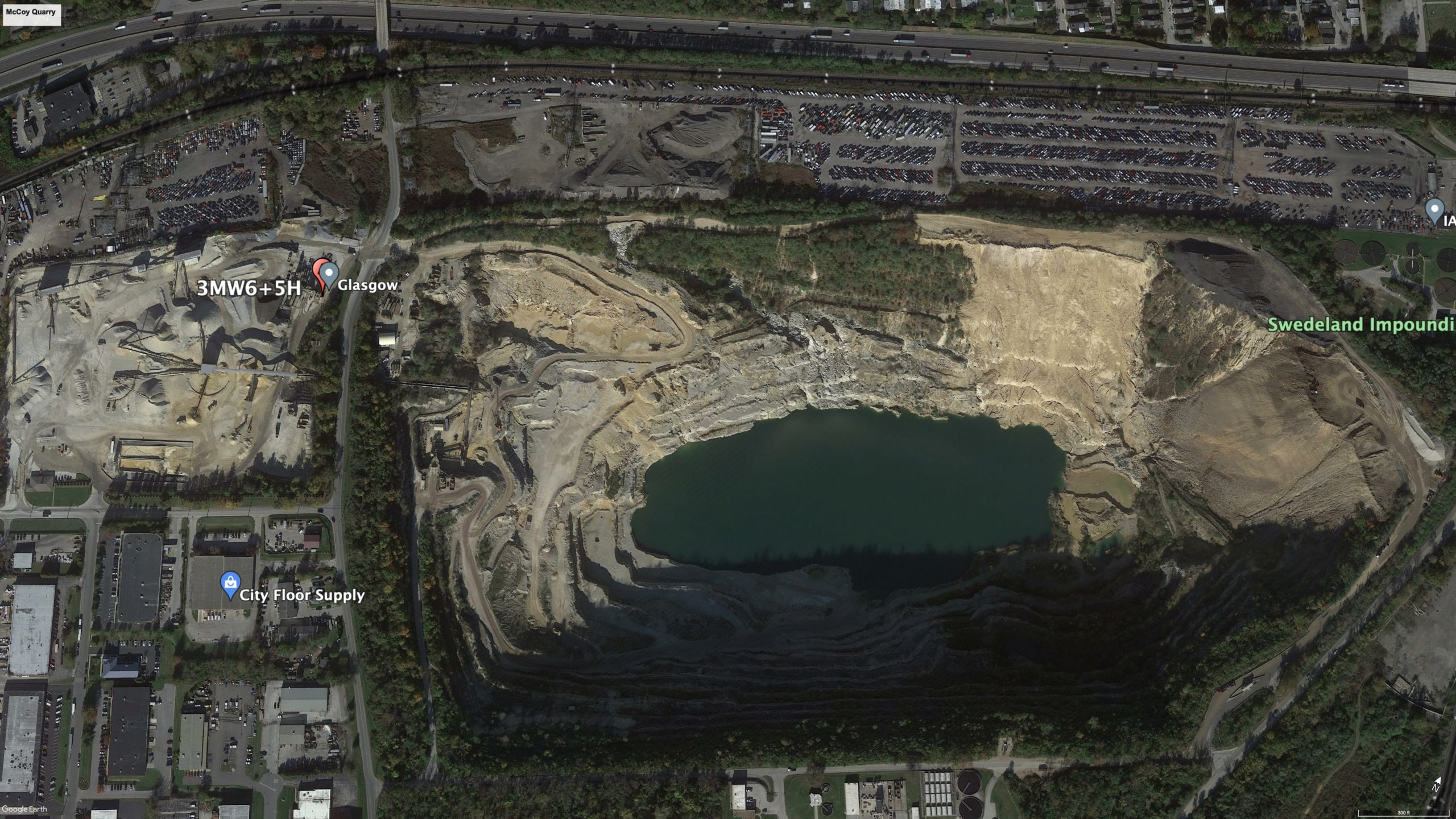
“We estimated about 4-5 million tons of material lied beneath pond,” explained Glasgow’s Vice President Jeff Frantz. “That section of material alone adds about seven years of production.”
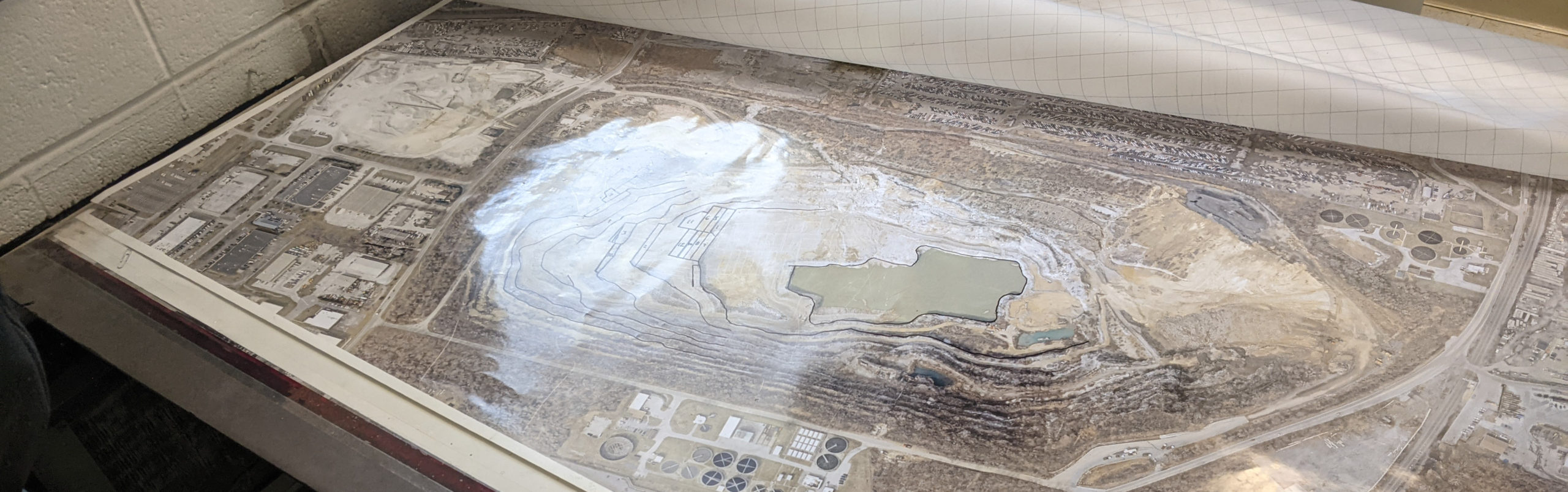
Solution:
In February 2020, Glasgow contacted Clearwater with interest in removing fines from their process water without a settling pond.
“We looked at belt presses, and I had visited a few sites with them, but they require a lot of maintenance and attention. Plus, they’re very expensive,” said Jeff.
“I came across Clearwater online and happened to see the High Compaction Clarifying Thickener, and it seemed interesting,” added Jeff. “I made a phone call and connected with Joe, who started working with me to determine feasibility.”
Clearwater’s Senior Application Engineer, Joe Lamb, worked with Glasgow to understand their problem and site layout. “The Glasgow project presented several interesting application challenges,” says Joe. “The primary wash plant lies well below and far from the clarifier location. They have clay veins in the quarry and three wash plants that operate together and independently throughout the day, which changes the flowrate, solids concentration, and solids consistency.”
Clearwater collected process water samples to understand the fines’ solids loading and size gradations. Jar testing determined the proper coagulant and polymer flocculant chemistry to expedite the settling velocity of the solids. Finally, settling velocity tests verified the settling and compaction rates and underflow densities for a clarifier.
This information coupled with a flowrate of 1,800 GPM allowed Clearwater to design a process water treatment system that allowed Glasgow to remove their settling pond. The clarifier system included a sump, slurry pumps, CW1400HC clarifier, LQ50 coagulant system, M800SS dry polymer system, AutoFloc Dosing System, dry polymer dilution water filtering system, and two mud cells with a sump.
However, Glasgow’s site setup created two challenges. First, the primary wash plant lies 90 ft below and 1,150 ft from the clarifier location, creating 125 TDH. A massive clean water distribution and slurry collection system required Clearwater’s design to meet this historical constraint. Second, they wanted to use the clarified water as dilution water for their dry polymer preparation because well water was not available and city water was too costly.
To meet the demands of the site setup, Clearwater designed a 2,250-gallon sump with two 75 HP slurry pumps in series to reach the clarifier. The tank level is automated via an ultrasonic level transducer, and onsite tuning yielded a signal that automates both pumps.
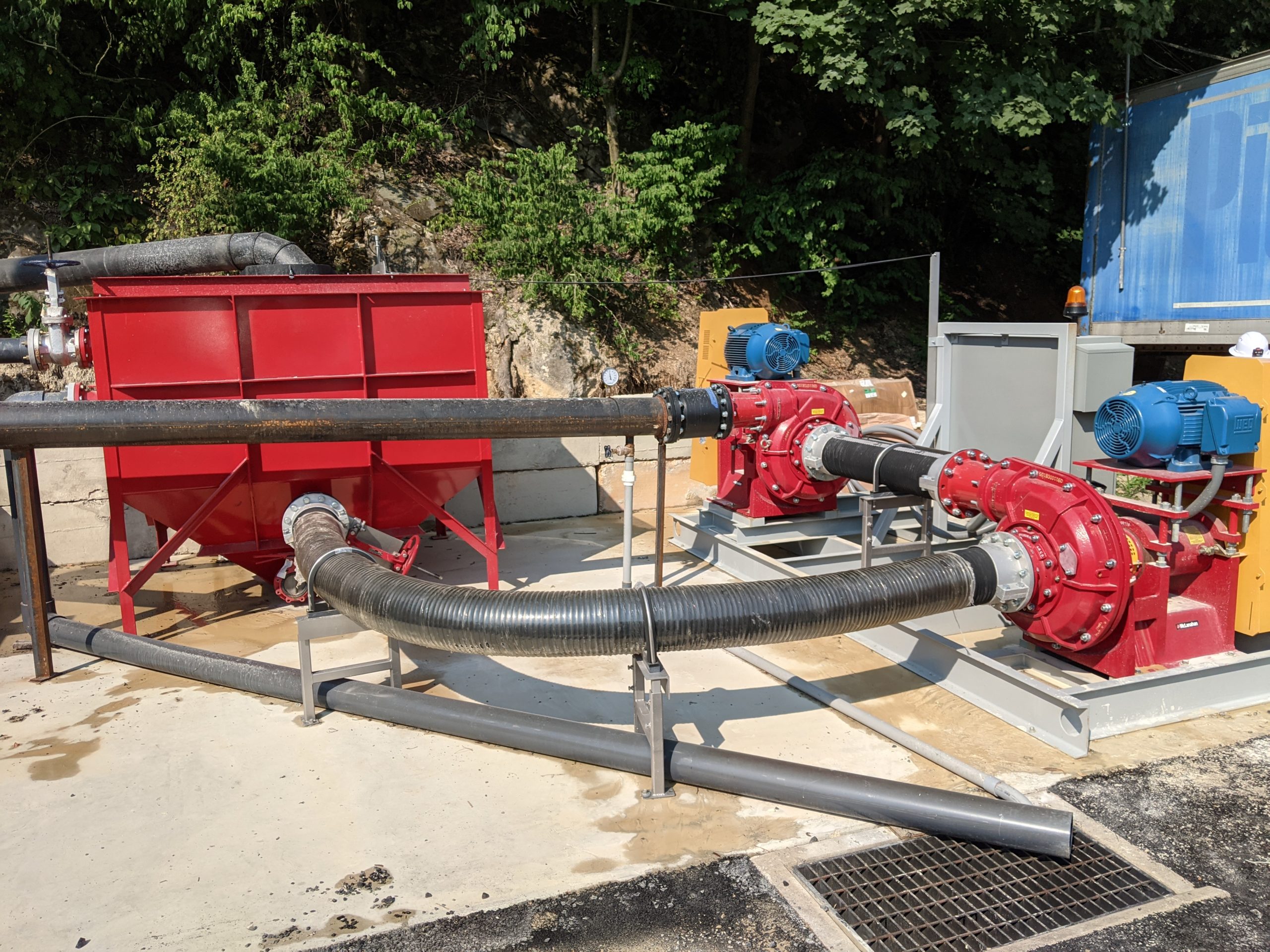
To use the clarified water as dilution water for the M800SS Dry Polymer Make-Down System, Clearwater installed two bag filters and one 30-micron cartridge filter. The filters guarantee clean dilution water to prepare an efficient and uniform polymer solution.
The sump and slurry pumps feed continuous dirty water to the CW1400HC Clarifying Thickener. The CW1400HC employs automated sensor technology to control continuous sludge level monitoring and evacuation.
The LQ50 prepares and doses a coagulant into the clarifier’s slurry influent line. And the M800SS prepares a dry polymer into a liquid flocculant solution and doses in the clarifier center well.
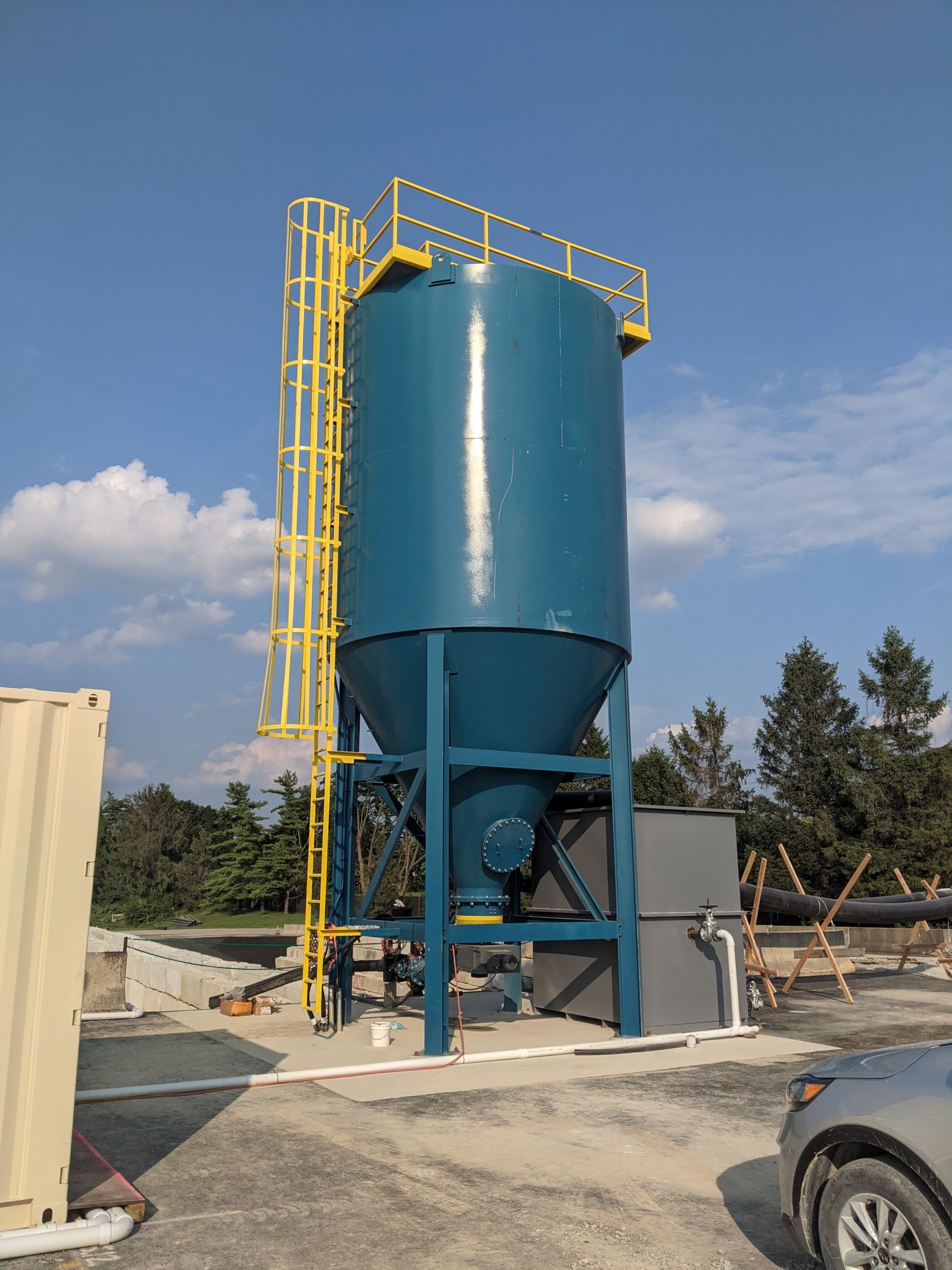
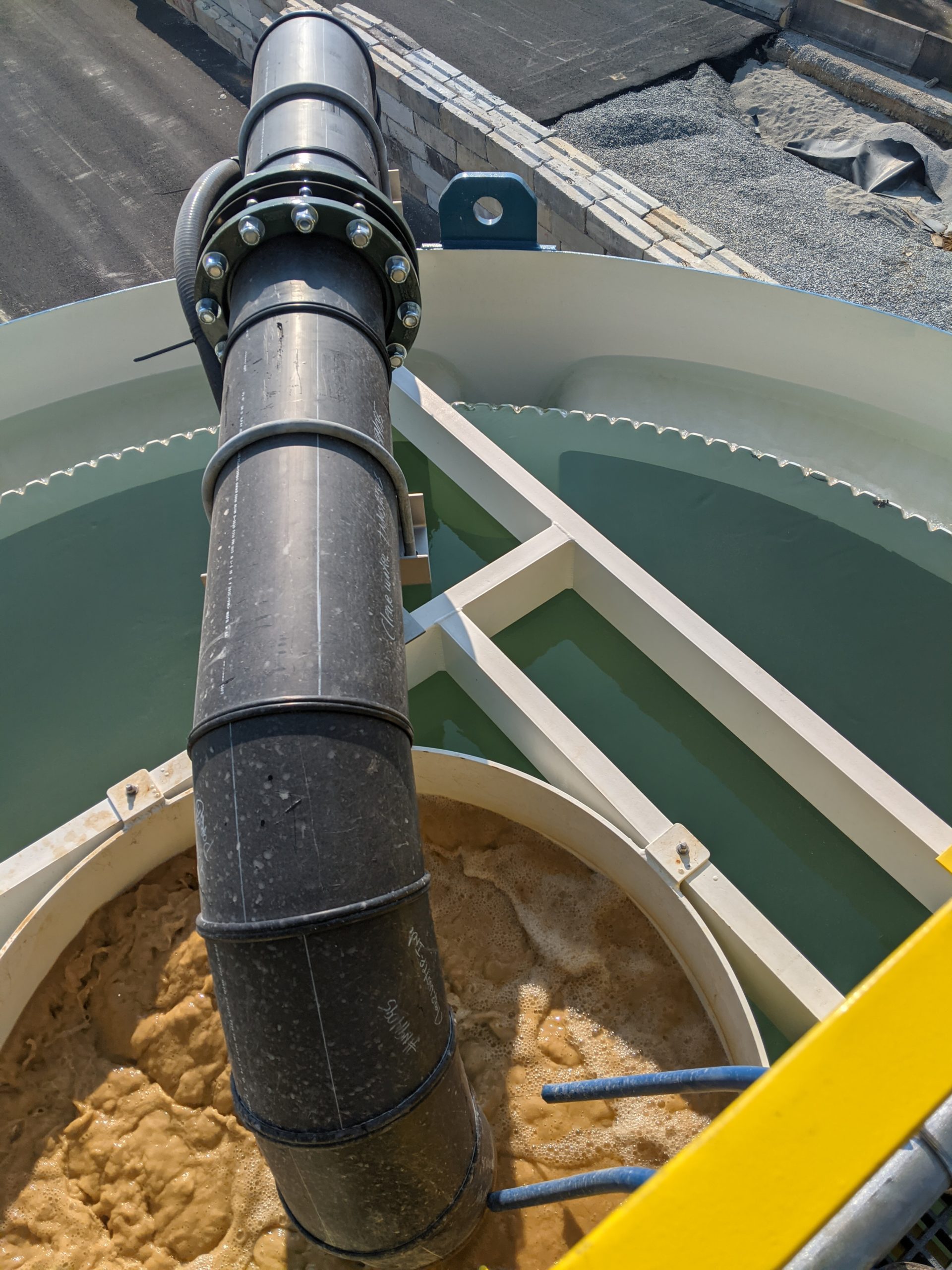
Clarified water overflow from the clarifier flows to a 3000-gallon stage tank before returning to the production process.
Mud underflow from the Clarifying Thickener flows into two mud cells, where it continues to dewater. Decant water from the dewatered mud falls to a sump and pumps back to the clarifier.
Results:
Glasgow eliminated their settling pond with Clearwater’s CW1400HC Clarifying Thickener and complete water treatment system.
By removing their settling pond, Glasgow can now access 4-5 million tons of material totaling about $48,000,000-$70,000,000 at today’s tonnage value.
“Once the clarifier system was operating, we reclaimed the settling pond space and started accessing the new material,” said Jeff.
The Clarifying Thickener produces a thick mud of about 55%+ solids by weight that dewaters quickly in the mud cells. The dewatered material is much easier to handle and reduces Glasgow’s material handling costs and time.
Jeff notes, “We started up, I believe, the end of March, maybe beginning of April, and we cleaned the first mud cell last week and started cleaning the other one this week. So, we ran that long before cleaning.”
Glasgow ran for eight weeks before cleaning out its first mud cell. Using two mud cells allows one to dewater while the other fills.
“We used a dragline to clean the old pond about once a week, and we’d have to handle the material twice due to the time it took to dewater. Whereas the mud from the cells is loadable, so we put it on a truck and dump it over one of the quarry’s high walls for reclamation. It’s a lot easier,” added Jeff.
Lastly, Glasgow can reuse its process water in a closed-loop clarification system.
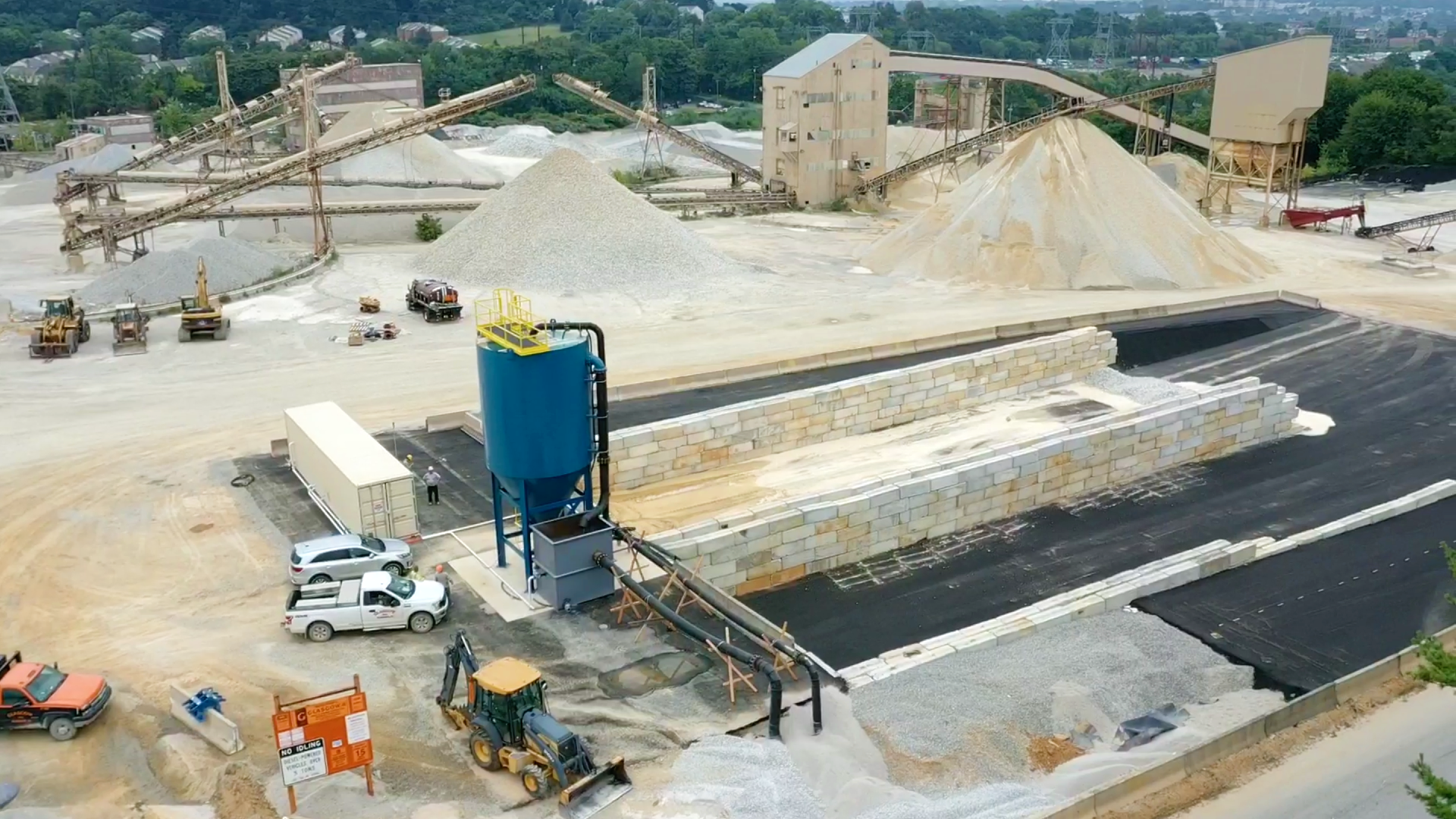
“It’s been a good relationship with Clearwater,” says Jeff. “We’ve had good communication, and if we have an issue, they’re quick to answer our call and support us as needed.”